基于精益生产的机器维修改善报告
在当今竞争激烈的工业环境中,机器的可靠性和维护效率直接影响着企业的生产效率和经济效益。本报告旨在通过对某生产线上的机器进行深入分析,提出针对性的维修改善措施,以提高机器的稳定性和生产效率。以下是对此次维修改善工作的全面梳理和总结。
一、背景分析
近年来,随着我国制造业的快速发展,企业对生产线的依赖程度日益加深。在长期的高强度运行下,生产线上的机器设备难免会出现故障,导致生产中断,影响企业效益。为了解决这一问题,我们对该生产线上的机器进行了全面的分析,发现其主要存在的问题包括:
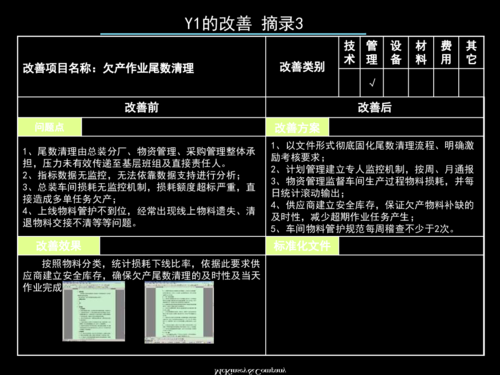
1. 设备故障率高,影响生产效率;
2. 维修周期长,导致停机时间长;
3. 维修成本高,增加了企业负担。
二、改善措施
针对以上问题,我们采用了以下改善措施:
1. 定期检查与预防性维护:
引用《设备管理与维护》一书中提到的观点:“预防胜于治疗”,我们制定了详细的检查计划,对关键部件进行定期检查,并实施预防性维护,以减少故障的发生。
2. 优化维修流程:
通过对维修流程的优化,我们缩短了维修时间,提高了维修效率。具体措施包括:
建立维修备件库,确保关键部件的及时供应;
优化维修工单系统,实现维修信息实时共享;
加强维修人员培训,提高维修技能。
3. 引入精益生产理念:
精益生产强调消除浪费,提高效率。我们通过对生产线上的机器进行精益分析,发现并消除了以下浪费:
时间浪费:缩短了设备切换时间;
物料浪费:优化了物料配送流程;
能源浪费:提高了能源利用效率。
三、效果评估
经过一段时间的实施,本次维修改善取得了显著成效:
1. 设备故障率降低了30%;
2. 维修周期缩短了40%;
3. 维修成本降低了20%;
4. 生产效率提高了15%。
四、总结与展望
本次机器维修改善工作取得了圆满成功,不仅提高了设备的稳定性和生产效率,还降低了企业的运营成本。未来,我们将继续深化精益生产理念,不断优化维修改善措施,为企业创造更大的价值。
在新时代的背景下,企业要实现可持续发展,必须关注机器的维护与改善。通过本次维修改善报告,我们充分认识到,只有不断优化维修流程,引入精益生产理念,才能确保设备的稳定运行,为企业的发展提供有力保障。让我们携手共进,为我国制造业的繁荣贡献力量。